Wir formen Ihre Lösung.
Als Spezialist für Kaltumformung überzeugen wir durch ganzheitliche und maßgeschneiderte Lösungen – von der Prozessentwicklung über den Maschinenbau bis hin zum fertigen Produkt in der Komponentenfertigung. Wir nennen das Make & Buy!
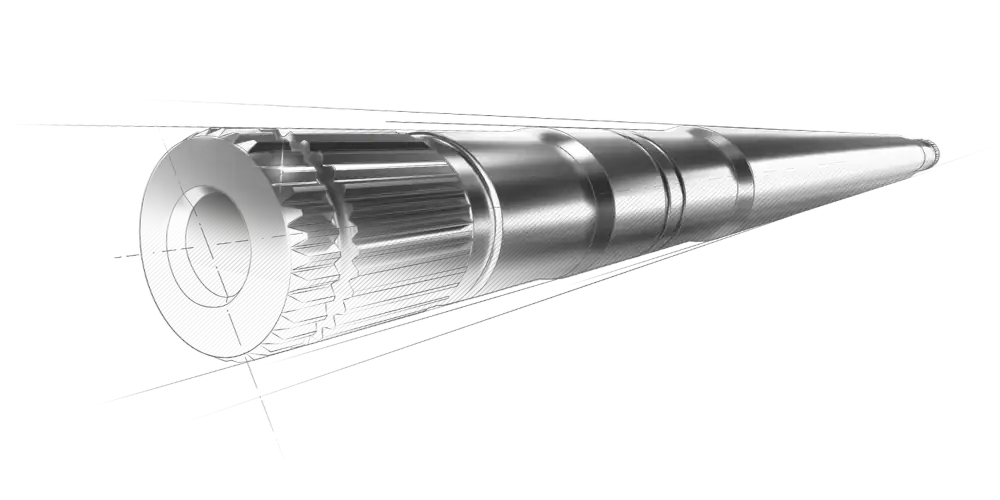
Ganzheitliche Kompetenz für Kaltumformung
Egal, was Sie brauchen – ob Prototypen, Großserien oder das Werkzeug dafür – wir sind Ihr Ansprechpartner. Von der Prozessentwicklung über den Maschinenbau hin zum fertigen Produkt in der Komponentenfertigung. So gewährleisten wir Ihre maßgeschneiderte Fertigung:
Wir nennen das Make & Buy!

Make
Maschinenbau bei uns heißt: exakt auf Ihre Anforderungen zugeschnittene Prozesse.
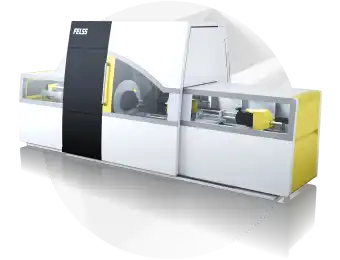
Buy
Komponentenfertigung: Präzise und hochkomplexe Bauteile, ready-to-install.

Technologien
Wir setzen auf modernste Verfahren für innovative Fertigungslösungen.
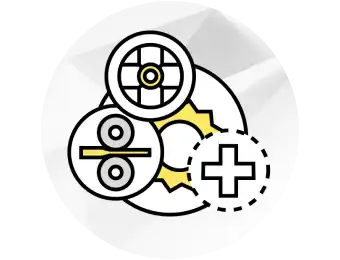
Industrie 4.0
Unsere Smart Services für effiziente Gestaltung und Optimierung komplexer Umformprozesse.

Service
Beratung, Wartung, Inspektion – unsere Services sind so individuell wie Ihre Bedürfnisse.

Maschinen
Wir bieten maßgeschneiderte Programme für jedes Wissensniveau vom Kaltumformexperten.

Ihr Projekt ist bei uns in besten Händen
Nockenwelle
Crashrohr
Hohlwelle
Antriebswelle
Lenkspindel
Lenkwelle
Sie haben Fragen zur Kaltumformung oder möchten sich beraten lassen?
Dann zögern Sie nicht, sich direkt an uns zu wenden. Ob es um Anliegen rund um Ihr anstehendes Projekt geht oder Sie mehr Informationen zu unseren Produkten und Dienstleistungen wünschen, wir freuen uns auf Ihre Herausforderung!

Abwechslungsreiche Aufgabenfelder in einer internationalen Unternehmensgruppe
Möchten Sie gemeinsam mit einem engagierten Team ressourceneffiziente Kaltumformlösungen gestalten und damit zu mehr Nachhaltigkeit beitragen? Bei Felss bieten wir vielfältige Stellenprofile in der Industrie und in der Mobilitätsbranche. Gestalten Sie die Zukunft mit uns – Ihre Ideen und Ihr Engagement machen den Unterschied.

Kaltumformung – Die Technik für komplexe und hochpräzise Fertigung
Bei Felss steht Kaltumformung für mehr als nur eine Fertigungstechnik – es ist die Kunst, Metall mit Präzision und Effizienz zu formen. Unsere fortschrittlichen Kaltumformungsprozesse nutzen die neuesten Technologien, um Metall bei Raumtemperatur zu formen, wodurch eine signifikante Material- und Energieeinsparung erzielt wird. Diese Technik ist nicht nur kosteneffizient, sondern verbessert auch die Materialstärke und Oberflächenqualität Ihrer Komponenten.
Enge Maßtoleranzen und hohe Festigkeit – Darum Kaltformung
Unter Kaltumformung versteht man die Umformung von Metall durch große Druck- und Zugkräfte. Dafür werden keine hohen Temperaturen benötigt, wodurch ein erheblicher Energieaufwand eingespart wird. Gleichzeitig führt das Verfahren zu einer erhöhten Festigkeit, die eine hohe Präzision in der Herstellung ermöglicht. Das macht die Kaltumformung zur idealen Technik um komplexe und hochgenaue Komponenten, wie sie in der Automobilindustrie und anderen technologieintensiven Sektoren benötigt werden, zu fertigen.


Sie haben eine Projektidee, die Sie umsetzen möchten? Wir unterstützen Sie.
Wir stehen Ihnen bereits in der Entwicklungsphase mit Rat und Tat zur Seite – und tun das auch noch nach Fertigstellung der Bauteile durch Service und 24/7-Betreuung.